Introduction
In today’s throat cutting competitive market, delivering a good quality product and services at an affordable price is a big challenge. We closely work with many solar EPC (Engineering, Procurement, and Construction) companies as their design partners. To deliver a cost-effective and energy-efficient solution, solar power plant design & engineering work plays a vital role. Every site comes with a new unique challenge and new opportunities that excite us more.
Case Study
One of our pharmaceutical industry owners from Vadodara wanted to go solar. He has an average consumption of electrical energy of 33,300 kWh per month which costs him approx 2.5 lakh per month, and he noticed a continuous increment in energy charges every year, so finally, in June 2019 they decided to install solar panels on his pharma factory.
Procedure Of Our Working
We met the client to understand their exact needs and did a detailed discussion. In the conclusion of the meeting, we found the following significant challenges:
- ROI (Return Of Investment) time of the project should be less than four years.
- Minimum project cost
- Maximum energy generation
- Minimum roof space should be occupied.
- Maximum strength & stability which can sustain with heavy winds.
After getting these challenges, we visited the site. The rooftop of the industry was divided into two parts,
1) RCC (Reinforced Cement Concrete) building and
2) A TIN shed having slope toward east and west (5 degrees).
However, to meet the above challenges, we worked on the selection of technology, project feasibility. We found that there are ventilators and few other objects which will cast a shadow on solar modules in the morning and evening time for a few months of winter. For us, each ray of sun is vital, and we wanted to get maximum radiation on solar panels.
Site Views
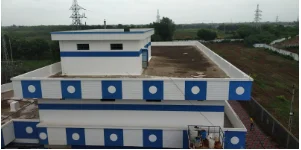
Solar Power Plant Design & Engineering
To get maximum generation, we can use MONO PERC (Passivated Emitter and Rear Cell) panels, which require less space and produce more energy at the same time. In addition, MONO PERC ( Passivated Emitter and Rear Cell) modules cost a lot more. After that, we studied the detailed datasheet of solar cell and chose modules in polycrystalline technology and fill factor of 79%. For instance, Poly 325-watt modules were good enough cost-wise and efficiency-wise.

Now the concern was space, Poly panels occupy more space and will cover almost complete RCC (Reinforced Cement Concrete) roof and TIN shed roof. The customer did not agree to cover the entire RCC (Reinforced Cement Concrete) roof, and he wanted some space for future construction on RCC (Reinforced Cement Concrete). However, it was a minor shadow, and we did not want to install solar panels in the shadow region on the TIN shed because we know it affects the generation of an entire row of panels, which was going to increase the ROI (Return Of Investment) time.
Process
We designed a complete 3D model of the site and simulated the entire project in software. Moreover, observed that we install the maximum project on the TIN shed, we will lose 5 – 7% energy because of the shadow of an air ventilator. We obviously can not remove the air ventilators of the industry. Therefore, we started looking for the best options for the inverter, which should have a maximum number of MPPT(Maximum Power Point Tracking) and maximum conversion efficiency. We were getting a maximum of 8 MPPT (Maximum Power Point Tracking)string Inverter for 126 KW project. We went a step ahead and decided to use an optimizer, which can provide an MPPT circuit per two solar panels, which reduces the losses further. With SolarEdge Inverter, we can make a string of 34 panels, which helps to reduce DC losses furthermore. Additionally, we can monitor each module’s performance from our IoT based remote monitoring system.
Designs Containing Different Factors

In other words, for the long life of the structure, we designed a complete Nut-bolting structure of HDGI material. Our structural engineer has simulated the design in Staad pro software and gives assurance of 150kmph withstand against winds.
Similarly, we measured earth resistivity and designed the grid of earthing in such a way that enabled us to achieve very low resistance (< 0.3 ohms) with less number of earthing rods. In addition, we calculated detailed losses of AC cable and chosen to optimize size & type.

Team Heaven
Once we got final approval from the design team, we sat in a meeting with the EPC company and the industry owner. In addition, we explained all the technical details of the project. He was delighted with this kind of in-depth analysis and optimized solution of the solar power plant. After that, he approved further installation. We prepared all the electrical drawings for CEI(Certified Electrical Inspector)approval and submitted it to the DISCOM. Above all, we prepared complete BOM (Bill of Materials)and working drawings for the installer.
Finally, the project got installed as per the drawings and commissioned recently. Our team inspected the site and checked the electrical parameters. In conclusion, the plant is working as expected, and hopefully, ROI will be done before 3.75 years. In other words, this project helped us to build stronger business relations with our client EPC company.
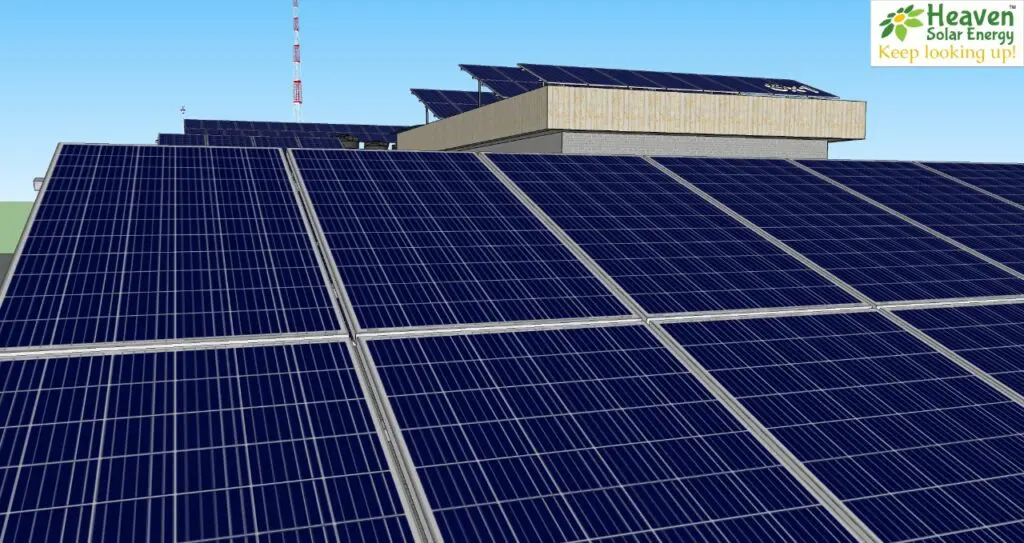
3D Design & Real Installations
To get solar power plant design solution contact us now.
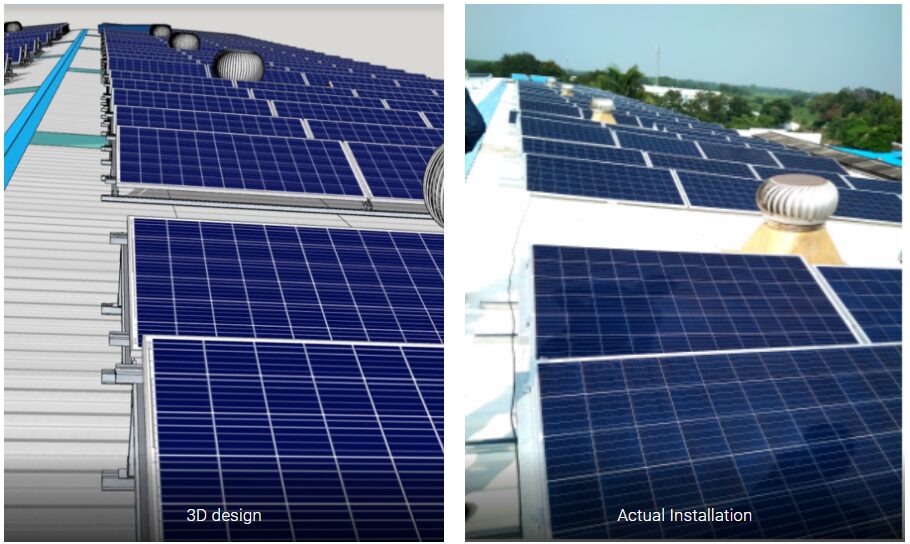
To get solar power plant design solution contact us now.